Fermentation Converts Greenhouse Gases into Useful Chemicals
According to the International Energy Agency, the chemical industry is the single largest industrial consumer of oil and gas, as well as the third-largest carbon emitter, emitting just under a gigatonne of CO2 in 2020.
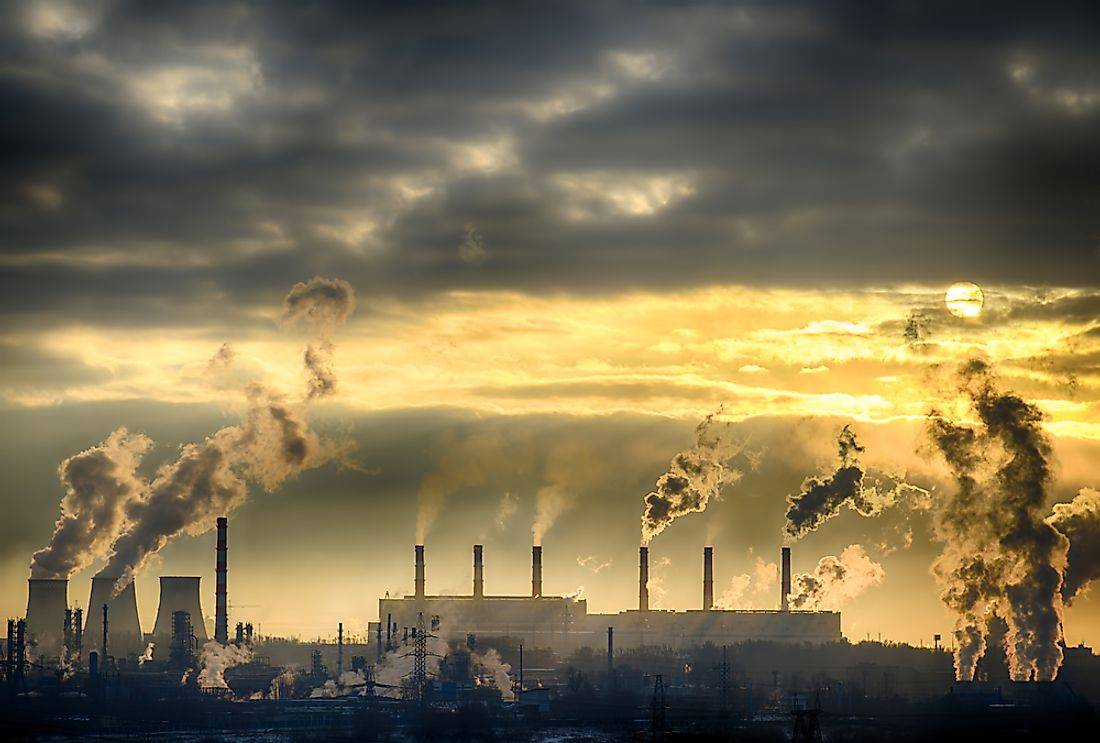
Researchers in the United States have developed a carbon-negative process for producing industrial-scale quantities of acetone and isopropanol. Their research could lead to the replacement of some high-emissions chemical production methods with more flexible and environmentally friendly processes.
According to the International Energy Agency, the chemical industry is the single largest industrial consumer of oil and gas, as well as the third-largest carbon emitter, emitting just under a gigatonne of CO2 in 2020.
Acetone and isopropanol (IPA) are two widely used commodity chemicals that are used as industrial solvents and platform chemicals in the production of materials, with a combined global market value of $10 billion.
Unfortunately, they are made from fossil resources using highly energy-intensive techniques that generate hazardous waste and greenhouse gas emissions (GHG).
As the climate crisis worsens, researchers are looking for ways to reduce the environmental impact of producing these commodities. A new paper in Nature Biotechnology describes the first report of high-production-rate, high-selectivity, and industrially scalable acetone and IPA fermentation.
Production by Fermentation
Acetone and IPA are typically produced through the cracking and reforming of propene, both of which are energy-intensive processes with no green alternatives. Scientists have developed methods for biomanufacturing substances through sugar fermentation. Natural enzymes and microorganisms are used to metabolize these sugars and produce the desired products.
However, current techniques have low yields and selectivity, making commercialization impossible. Instead, the new study looked at autotrophic production as a starting point, using waste resources like carbon oxides (carbon monoxide or carbon dioxide) from heavy industry or syngas from biomass resources.
The collaborative research team from LanzaTech Inc., Northwestern University, and Oak Ridge National Laboratory, led by Ching Leang, Michael Jewett, and Michael Köpke, achieved industrially relevant productivities of up to about 3 g/l/h with continuous production over about three weeks and high selectivities of up to 90 percent.
These results are in stark contrast to previous leading rates of 3.8 mg/l/h and 1.2 percent selectivity. The collaborative research team from LanzaTech Inc., Northwestern University, and Oak Ridge National Laboratory, co-led by Ching Leang, Michael Jewett, and Michael Kopke, achieved industrially relevant productivities of up to 3 g/l/h with continuous production over about three weeks and high selectivities of up to 90%. These findings contrast sharply with the previous leading rates of 3.8 mg/l/h and 1.2 percent selectivity.
Optimizing Fermentation Pathway
The team concentrated its efforts on optimizing the fermentation pathway, microbe strain, and process to achieve such high efficiencies.
The team began by identifying the best set of pathway enzymes to carry out the fermentation, first exploring a collection of nearly 300 biosynthetic genes for acetone production and then screening a library of C. autoethanogenum sAdh enzymes to convert acetone to IPA.
The chosen strain was then optimized to improve selectivity in production – that is, to eliminate unwanted byproducts. They identified and included several genetic modifications to edit the strain, including four gene knockouts and two gene overexpression. Until now, previous studies have only included one genome modification. These changes assisted the team in increasing the proportion of energy in the feed gas that went to the product of interest.
Finally, the team moved from a two-litre benchtop reactor to a 120-litre plant loop reactor. This step aided in demonstrating the process's scalability and identifying potential issues when transitioning from benchtop to industrial production. This size of a bioreactor, in particular, has spatial heterogeneities, which means that different zones of the reactor have different chemical compositions.
The researchers needed to assess the process's metabolic robustness, looking at how the microbes remained functional despite changes in gas substrate concentration. Their findings confirmed that the developed strains could be used on a large scale.
Greater Flexibility
Traditional chemical manufacturing plants are designed to handle a single process. Bioreactors, on the other hand, can be adapted to multiple purposes, providing valuable flexibility, particularly during economic downturns when the availability of certain commodities (such as ethanol and IPA in 2019) fluctuates.
Furthermore, from an environmental standpoint, gas fermentation is a promising approach. While traditional acetone and IPA production emit 2.55 kg and 1.85 kg of CO2 per kilogramme produced, respectively, gas fermentation is a carbon-negative process because it uses waste carbon products. The team's life cycle analyses revealed a negative carbon value; each kilogramme of produced acetone and IPA absorbed 1.78 kg and 1.17 kg of CO2, respectively.
According to the researchers, this contrast provides hope for replacing an emissions-intensive process with a circular economic model "in which carbon from agricultural, industrial, and societal waste streams is recycled into a chemical synthesis value chain and displaces manufacturing of products from fresh fossil resources."
(Source: Physics World)
Download Krishi Jagran Mobile App for more updates on the Latest Agriculture News, Agriculture Quiz, Crop Calendar, Jobs in Agriculture, and more.