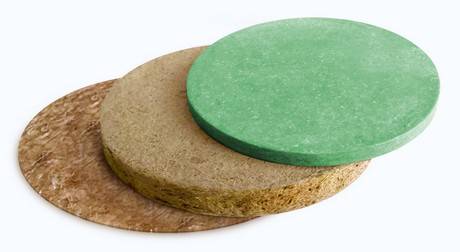
The need of the hour is to save the environment. Garbage is increasing with the rise in population. There are heaps of plastic wastage and mountains of the single use plastic everywhere. In order to solve this problem a company has come out with a unique solution.
They use plant wastes to manufacture new materials. The lettuce is used for the eating and the remains are useful for the making containers. The Company transfers their developed technology to Companies that produce or manage plant waste and Companies that want to use ecological materials in their manufacture .
Feltwood Raw Material is an alternative to plastic and wood. A competitive advantage for companies that wish to manufacture their biodegradable and recyclable products.
The food & agricultural system generates a large amount of plant waste, whose handling is costly & requires a management effort. However, that waste can also bring opportunities. Arancha Yáñez, CEO of Feltwood said, "The parts of lettuce or artichoke we don't eat, as well as other sorts of plant waste, go through an industrial process in order for new materials to be manufactured".
Yáñez said, "We have developed a technology that produces environmentally-friendly industrial materials from agricultural plant waste, without adding any plastic, adhesive or binder."
The technology of this company is based on two differentiated processes: firstly, plant waste is taken and transformed into Feltwood Raw Material. This is then molded to manufacture products that are 100 percent biodegradable, recyclable and even compostable.
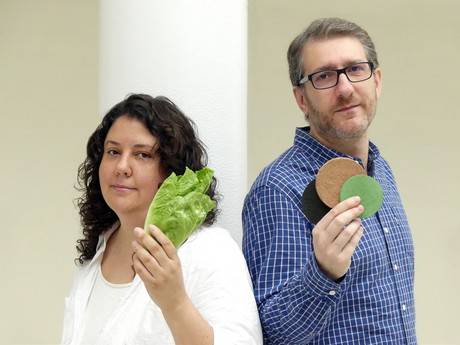
After years of research the company has developed the necessary technologies to transform plant residues into biodegradable industrial materials without toxins, which are a real alternative to plastic and wood in many applications. They do not contain plastics, adhesives or binders of any kind. The technology is available to producers and waste managers and companies looking for alternatives to manufacture their products with ecological materials.
Yáñez, has been a diver since she was a childhood. She believes that the alternatives to toxic and non-biodegradable materials, like plastic, need to have a competitive price, as well as be biodegradable and with optimal technical characteristics. She added “Our processes are modular, and materials with different technical properties can be obtained. This allows us to focus on more than one sector as a target market. After the validation of the first industrial plant, we aimed at a plan of rapid international expansion, taking advantage of the knowledge generated in that validation. The focus is in Europe, mainly the Nordic countries, as their legislation and customs make our technology attractive. Some multinationals have contacted us and we are reaching agreements for a quick internationalization while protecting our industrial property”.

The CEO said, “These materials are made 100 percent from plant fibers that we extract from more than 30 different sorts of plant waste, and we continue researching to add even more. The list of crops used includes lettuce, artichoke and pineapple, just to name a few.”
She said, “We have 3 materials with different characteristics for four specific markets, all fully biodegradable, recyclable and compostable: Feltwood Insulation, focused on the construction sector, cold rooms and modular roofs, among others; Feltwood Anti-Impact, with ideal properties for protective packaging; Feltwood Pack, for the light packaging industry (small boat-shaped containers) and Feltwood Hard, ideal material for applications that require great resistance, such as furniture.”